Digitalisierung
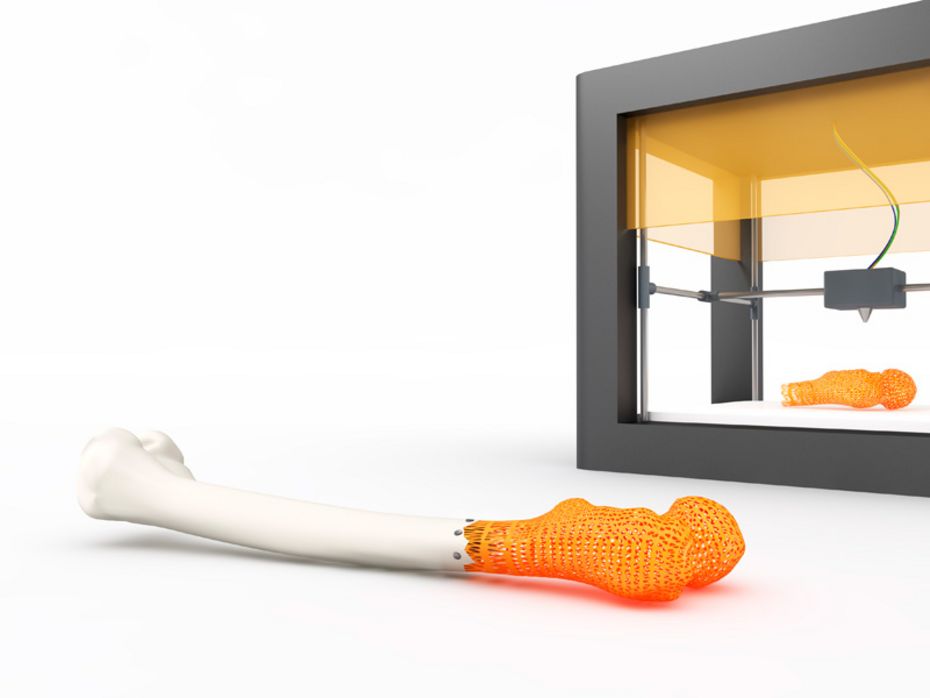
Neue Produktion
Vom 3D-Druck bis zu Big Data: Die Digitalisierung verspricht eine Industrie 4.0, die Ressourcen effizienter und damit produktiver als bisher einsetzt. Doch den Ressourcenhunger kann eine digitalisierte Produktion nur bremsen, wenn sie tatsächlich erfasst, wieviel sie wofür benötigt. Davon sind die meisten Unternehmen in der Praxis noch weit entfernt.
Von Verena Kern
Anfang der 1980er Jahre hatte Chuck Hull genug vom Warten. Der Technische Direktor eines kunststoffverarbeitenden Unternehmens in San Gabriel, Kalifornien, ärgerte sich immer wieder über langwierige Verzögerungen bei der Entwicklung neuer Bauteile. Bis aus einem Entwurf endlich ein Prototyp hergestellt war, vergingen viele Monate. Technisch war dies damals nicht anders möglich. „Das war ein großes Problem“, sagt der Physikingenieur. „Es dauerte zu lange.“
Hull wollte Zeit sparen, die Fertigung beschleunigen. Die Idee, auf die er schließlich kam, war so radikal wie einfach. Er stellte die bisherigen Verfahren quasi auf den Kopf. Anstatt Material abzutragen und so zunächst mit großem Aufwand eine Form herzustellen, in die das entworfene Teil gegossen werden kann, entschied Hull sich für den umgekehrten Weg: einen Gegenstand Schicht für Schicht aufzubauen.
Nötig war dafür nichts anderes als ein geeigneter Kunststoff, ein Laser und ein Computerprogramm. Dieses steuert den Laser, der wie der Kopf eines Tintenstrahl-Druckers in einem Bad aus lichtempfindlichem flüssigen Kunststoff die Stellen abfährt, die Teil des neuen Gegenstands werden sollen. Dort härtet der Kunststoff aus. Dann fährt der Laser die nächste Lage ab und so weiter, bis der komplette dreidimensionale Körper entstanden ist. „Es war“, sagt Chuck Hull, „ein magischer Moment“, als er das erste Objekt mit seinem neuen Verfahren herstellte, eine Augenmuschel für den Optikerbedarf. „Ich war damit in der Lage, die digitale Welt mit der echten Welt zu vernetzen.“
Stereolithografie nannte Hull seine Erfindung, für die ihm 1986 das Patent 4,575,330 erteilt wurde. Die Bezeichnung 3D-Druck setzte sich erst später durch.
Doch das Verfahren führte lange Zeit nur ein Nischendasein. Es wurde zunächst vor allem für die Herstellung von Prototypen und Modellen eingesetzt, war auf die Verarbeitung von Kunststoffen beschränkt und vom Einsatz in der industriellen Fertigung meilenweit entfernt. Hull selbst brauchte mehrere Jahre, bis er genug Startkapital für eine eigene Firma zusammen hatte. Erst in den 1990er Jahren flossen erste Gewinne.
Additiv statt abrasiv
Dabei gilt das 3D-Drucken inzwischen als „Wundertechnik“ mit dem Potenzial, eine neue industrielle Revolution auszulösen. Schließlich ist es damit möglich, praktisch jede denkbare Form herzustellen, und das auf ganz einfache Weise. Selbst vollständige Häuser könnten so gebaut werden. Auch völlig neue und komplizierte Teile, bei denen die herkömmlichen Verfahren an ihre Grenzen stoßen, lassen sich fertigen. Gerade für den ressourcenschonenden Leichtbau hat das immense Vorteile.
„Sie müssen es sich so vorstellen“, sagt Frank Brückner. „Mit der additiven Fertigung können Sie sogar eine Kugel in einem Würfel herstellen. Das war vorher nicht möglich.“ Additive Fertigung ist der Fachbegriff für den 3D-Druck. Er bezieht sich darauf, dass Material nicht abgetragen, sondern aufgetragen, hinzugefügt wird.
Brückner arbeitet für das Zentrum Additive Fertigung des Fraunhofer-Instituts für Werkstoff- und Strahltechnik IWS in Dresden. Es ist das größte Zentrum für angewandte Forschung in diesem Bereich in Europa. Geforscht wird hier an der neuesten Entwicklung im 3D-Druck, dem Drucken aus Metall. Das IWS sieht darin einen Paradigmenwechsel in der Fertigungstechnik. Das Verfahren erlaubt „neue Freiheitsgrade“, Produkte können „losgelöst von den Grenzen der konventionellen Fertigungstechnik“ optimiert werden, die Produktion wird „in bislang unbekanntem Ausmaß“ flexibilisiert. Statt Metallteile zu gießen oder aus Metallblöcken herauszufräsen, werden sie aus pulver-, pasten- oder drahtförmigem Metall und per Laser hergestellt. Das spart viel Aufwand und Material. Auch die Kombination verschiedener Werkstoffe und damit verbesserte Produkteigenschaften werden so möglich
Gerade hat das IWS gemeinsam mit Rolls-Royce Deutschland eine innovative Schutzschicht für Flugtriebwerke entwickelt, mit der die Effizienz der Triebwerke verbessert wird. Mit einem hochpräzisen Laser werden metallische Mikrostrukturen aufgetragen, die für außergewöhnliche Haftfestigkeit sorgen, so dass die Schutzschicht mit höheren Arbeitstemperaturen belastet werden kann. Die Lebensdauer der Schicht erhöht sich, die Bauteile müssen seltener gewartet werden. Bei Rolls-Royce läuft die Anwendung nun in der Serienfertigung, wird also in jedem neuen Triebwerk eingesetzt.
Besonders großes Interesse an der neuen Technik zeigen bislang die Luft- und Raumfahrt, die Medizintechnik und die Automobilindustrie. „Bei komplexen und hochpreisigen Teilen lohnt es sich natürlich am meisten“, sagt Brückner. Doch inzwischen wird es auch für den weniger hochpreisigen Bereich interessant. „Immer mehr Unternehmen kommen auf uns zu.“
Völlig verdrängen wird der 3D-Druck die bisherige Fertigungstechnik jedoch nicht. „Auch in einigen Jahrzehnten wird es noch traditionelle Verfahren geben“, sagt Brückner. „Die additive Fertigung ist eine Ergänzung, eine Erweiterung.“ Eine zusätzliche Möglichkeit also, aber kein Ersatz.
Fertigung bleibt ressourcenintensiv
Auch für den enormen Ressourcenhunger der Fertigungsindustrie liefert die neue Technik bei all ihren Vorzügen keine Lösung. Eine weitere, ergänzende Technologie wird kaum etwas daran ändern, dass die produzierende Industrie der mit Abstand größte globale Energieverbraucher ist. Gut 50 Prozent des Gesamtverbrauchs landen in ihren Fabriken, hat die US-amerikanische Energy Information Administration (EIA) in einer Studie errechnet. Damit steht die Fertigungsindustrie für gut die Hälfte des weltweiten Bedarfs an Kraftstoffen, Gas, Fernwärme und Strom. Auch die Wachstumsraten des industriellen Energiehungers sind überdurchschnittlich. In den vergangenen 40 Jahren wuchs ihr Verbrauch dreimal so schnell wie der Energieverbrauch insgesamt.
Bei solchen Größenordnungen ist jede Idee, wie Energie eingespart werden könnte, von Bedeutung. Die Siemens-Sparte Financial Services beziffert das Einsparpotenzial in Deutschland auf knapp 15 Prozent, in Großbritannien auf 14 Prozent und in Russland auf 19 Prozent. Nach Berechnungen der Internationalen Energieagentur IEA könnte die Industrie weltweit bis 2035 gut drei Billionen US-Dollar an Energiekosten einsparen, wenn sie gleichzeitig gut eine Billion investiert.
Doch um Effizienzpotenziale heben zu können, muss man erst einmal in der Lage sein, sie zu finden. Sprich: Wenn ein Unternehmen nicht erkennen kann, wo und wie in seinem Betrieb Einsparmöglichkeiten vorhanden sind, kann und wird es kaum etwas tun. Man braucht Daten. Man muss sie erheben, muss sie ordnen und auswerten, um, wie Siemens es ausdrückt, einen „sinnvollen Diätplan“ für die energiehungrige Industrie entwerfen zu können.
Mit der Digitalisierung sollte das eigentlich kein Problem mehr sein. Zumindest theoretisch. In der Praxis sieht es häufig anders aus. „Das größte Problem bei Effizeinzmassnahmen ist die intransparente und zumeist nicht ausreichende Datengrundlage.“ sagt Henning Sittel.
Sittel arbeitet für die Effizienz-Agentur NRW (EFA). Seit Jahren berät und begleitet er Unternehmen, die in ihrem Betrieb Ressourcen wie Material, Energie und Wasser einsparen wollen. Die Agentur geht auf die Firmen zu, wirbt für Effizienzmaßnahmen. Rund 150 Beratungsprojekte kommen so pro Jahr zusammen, sowie weitere 50 Finanzierungsberatungen.
Daten zur Veränderung
Doch nur die Hälfte der Unternehmen setzt die Projekte auch um. „Aber das ist eine gute Quote“, sagt Sittel. Der erste Stolperstein sind oft die fehlenden Daten. „Daten zu erheben, die Sie bislang nicht erhoben haben, ist mit viel Aufwand verbunden“, sagt er. „Sie müssen Leute dafür abstellen, Abläufe unterbrechen.“ Viele Firmen können das nicht leisten, hat der Berater festgestellt. „Die Betriebe sind mit ihrem Tagesgeschäft dicht.“ Sie haben keine Zeit und insgesamt keine Kapazitäten für zusätzliche Aufgaben übrig.
Ein Beispiel für eine erfolgreiche Beratung sind die Edelstahlwerke Schmees. Die Firma produziert am NRW-Standort Langenfeld mit 140 Mitarbeitern und im sächischen Pirna mit weiteren 170 Mitarbeitern Stahlgussteile für die Nahrungsmittel- und Pharmaindustrie sowie den Energiemaschinenbau. Die Ressourceneffizienzberatung der EFA half dem Unternehmen, seinen Material- und Energieeinsatz besser zu erfassen. So konnten Materialverschwendungen frühzeitig identifiziert und die Effektivität des Fertigungsablaufs verbessert werden. Insgesamt spart das Unternehmen so pro Jahr 130 Tonnen Stahl ein, reduziert seine Kosten um 400.000 Euro und senkt seinen jährlichen Ausstoß an CO2-Äquivalenten um fast 700 Tonnen.
„Es geht um viele kleine Bausteine“, sagt Berater Henning Sittel. Je mehr Unternehmen mitmachen, desto besser. „Das summiert sich.“ Den Firmen gehe es natürlich vor allem um die Kosten und um ihre Wettbewerbsfähigkeit. „Mehr Ressourceneffizienz und Klimaschutz sind dann quasi der Nebeneffekt.“
Allerdings beobachtet Sittel auch eine gewisse Beratungsresistenz in der mittelständischen Wirtschaft. Die Firmen wollen oder können nur wenig investieren, erwarten aber, dass sich die Maßnahmen schon in kürzester Zeit rechnen, diese sind jedoch in vielen Fällen als längerfristig anzusehen.
Und dann gibt es noch den menschlichen Faktor. „Es geht hier um Veränderungsprozesse“, sagt Sittel. „Und Menschen mögen keine Veränderungen, sie halten lieber fest an dem, was und wie sie es immer gemacht haben.“ Möglicherweise müsse man künftig auch Arbeitspsychologen mit ins Beratungsteam nehmen, um auch solche Schwierigkeiten auffangen zu können.
Systematisch bewerten und kennzeichnen
In einer groß angelegten Studie hat das VDI Zentrum Ressourceneffizienz kürzlich untersucht, wie viel das verarbeitende Gewerbe durch die Digitalisierung an betrieblichen Ressourcen einsparen könnte. Das fast 300 Seiten starke Papier zieht anhand zahlreicher Fallbeispiele eine ernüchternde Bilanz. Maßnahmen der digitalen Transformation bewirken zwar durchaus Einsparungen, so beim Stromverbrauch und Materialeinsatz, bei der Menge an Abfall und an innerbetrieblichen Transporten sowie an benötigtem Lagerraum. Wie groß diese Einsparung ist, lässt sich jedoch nur schätzen. Denn in den Unternehmen erfolgt „keine systematische Erfolgskontrolle zur Nachverfolgung und Quantifizierung der Ressourceneinsparungen“, heißt es in der Studie. Denn den Firmen geht es in erster Linie um die Verbesserung ihrer Wettbewerbsfähigkeit, etwa durch Prozessautomatisierung. Die Steigerung der Ressourceneffizienz ist keine Priorität und wird deshalb auch nicht gezielt analysiert und ausgewertet.
Genauso wenig wird erfasst, wie viele Ressourcen durch die Digitalisierung zusätzlich verbraucht werden – durch den Einsatz weiterer Hardware sowie durch den höheren Stromverbrauch des Betriebs von Hard- und Software. Beispielrechnungen zeigen indes, dass die zusätzlichen Aufwände die Netto-Einsparungen von Effizienzmaßnahmen reduzieren.
Gut möglich, dass die Digitalisierung die Wirtschaft nur scheinbar effizienter macht. Schon heute liegt der Energiebedarf von Telekommunikationsnetzen und Rechenzentren laut Bundesregierung bei 18 Terawattstunden. Dafür müssen rechnerisch etwa fünf mittelgroße Kohlekraftwerke Strom liefern. Bis zum Jahr 2025 allerdings dürfte der Bedarf auf 25 Terawattstunden steigen, das wäre ein Zuwachs von 39 Prozent. Der Energiebedarf der gesamten informations- und kommunikationstechnischen Ausstattung Deutschands – einschließlich Computern, Smartphones, Tablets und Co. wird laut Regierungsprognose bis 2025 gar auf rund 46 Terawattstunden anwachsen.
Die VDI-Studie empfiehlt der Politik deshalb eine ganz schlichte Maßnahme: die Entwicklung von Labeln beziehungsweise Kennzeichnungssystemen zur Angabe des Energieverbrauchs in diesem Bereich – damit überhaupt erst einmal die Daten vorliegen, die man für sinnvolle Effizienzmaßnahmen braucht. Höchste Zeit dafür wäre es.
Verena Kern ist freie Journalistin in Berlin. Ihre Schwerpunkte sind Umwelt-, Klima- und Energiethemen. Seit 2011 gehört sie zum Redaktionsteam des Online-Magazins klimareporter.de. Daneben schreibt sie für die Frankfurter Rundschau, Deutsche Welle und Fachmagazine. Im factory-Magazin Besser bauen (2-2017) schrieb sie zuletzt über Bauen mit (Ressourcen)-Bewusstsein.
Weitere Beiträge zur Digitalisierung und ihren möglichen Wirkungen auf Ressourcen- und Klimaschutz, auf soziale Gesellschaften und Individuen gibt es im gleichnamigen factory-Magazin Digitalisierung. Das ist reich illustriert und enthält sämtliche Artikel im kompakten Tablet-Format, dazu entsprechende Zahlen und Zitate. Es lässt sich kostenlos laden und ist angenehm lesbar auf Bildschirmen und Tablet-Computern. Online im Themenbereich sind zunächst nur einige Beiträge verfügbar – dafür lassen sie sich dort auch kommentieren und bewerten.
Beiträge online
News zum Thema
- 05/2023 | Vollzeitarbeitende wünschen sich Viertagewoche
- 09/2022 | Digitalisierung muss stärker dem sozial-ökologischen Wandel dienen
- 08/2022 | Wie Unternehmen mit KI nachhaltiger wirtschaften
- 07/2022 | Förderprogramm DigiRess zur Digitalisierung der Ressourceneffizienz in zirkulären Produktionsprozessen
- 06/2022 | Verantwortungsvolle Unternehmen sollten Effizienzgewinne für weiteren Klima- und Ressourcenschutz einsetzen
- 06/2022 | Solar Decathlon Europe 21/22 zeigt Beispiele für ressourcenschonendes urbanes Bauen
- 12/2021 | Klimaschutz im Koalitionsvertrag: Ambitioniert, aber nicht genug – besonders bei Gebäuden, Landwirtschaft und Verkehr
- 11/2021 | Eine Industrieregion will klimaneutral werden: Die "zeero-days" zeigen wie
- 09/2021 | Scheinlösungen führen nicht zu mehr Klimaschutz
- 08/2021 | So kann das Ruhrgebiet zur grünsten Industrieregion der Welt werden
- 06/2021 | 30 Jahre Wuppertal Institut: Die Suche nach den besten Hebeln für den Wandel
- 05/2021 | Wie eine neue Bundesregierung die Umwelt- und Klimaziele bis 2030 und 2045 sozial und ökologisch gerecht erreichen kann
- 02/2021 | Studie zu Unternehmen in der Coronakrise: Personalabbau statt Ressourceneffizienz
- 12/2020 | Deutscher Nachhaltigkeitspreis 2020 mit Liveübertragung und virtuellem Kongress
- 10/2020 | Wie Deutschlands Energiesystem bis 2035 CO2-neutral und das 1,5-Grad-Ziel erreicht werden kann
- 09/2020 | Digitalisierung entkoppelt Wirtschaftswachstum bislang nicht vom Energieverbrauch
- 08/2020 | CO2-Bilanzierungstool ecocockpit in neuer Version online
- 07/2020 | Corona-Folgen: Neue Arbeits- und Zeitmodelle für mehr Ressourcenschonung
- 07/2020 | Zukunft Für Alle-Kongress mit über 200 Veranstaltungen zu Utopien und Transformation
- 06/2020 | Ökobilanzen sind der erste Schritt für bessere Elektronikprodukte
- 06/2020 | Deutsche sehen in Digitalisierung nach den Corona-Erfahrungen mehr Chancen für die Umwelt
- 04/2019 | Ungestaltete Digitalisierung ist Brandbeschleuniger beim Ressourcenverbrauch
- 04/2019 | Deutschlands Klimabilanz 2018: Wegen warmer Witterung 4,2 Prozent weniger Treibhausgasemissionen
- 03/2019 | Weltweit steigender Ressourcenverbrauch treibt Klimawandel und Artenverlust
- 03/2019 | Globale UN-Vereinbarung gegen Plastikmüll gefordert
- 02/2019 | Ranking der Nachhaltigkeitsberichte: KMU und Großunternehmen berichten besser über Lieferketten
- 01/2019 | Remanufacturing als Geschäftsmodell zur Rohstoffeinsparung
- 01/2019 | Agrarpolitik: Subventionen für das Falsche
- 12/2018 | Klimaschutz selbermachen: Energieverbrauch prüfen und senken
- 11/2018 | Wie sich das Klimaziel 2030 sicher erreichen lässt
- 11/2018 | Was haben Bits mit Bäumen zu tun?
- 09/2018 | Verkehrswende: Ab 2028 darf die EU keine Benziner und Diesel mehr zulassen, wenn sie ihr Klimaziel erreichen will
- 09/2018 | Ressourceneffizienz: Die nächsten 20 Jahre
- 09/2018 | Der Stand der Ressourceneffizienz in der Industrie 4.0
- 07/2018 | Digitalisierung für die Circular Economy
- 07/2018 | Ressourceneffizienz in Wertschöpfungsketten: Da geht viel mehr
- 06/2018 | In zehn Jahren machen Roboter die Hälfte der Bürojobs – mit einer Rendite von bis zu 1000 Prozent
- 06/2018 | Ein Tag des guten Lebens für alle
- 05/2018 | Carbon-Footprint für Unternehmen: CO2-Bilanzierung mit dem ecocockpit
Themen
- Kapital
- Wohlstand
- Design
- Ressourcen
- Klimaneutral
- Industrie
- Vielfalt
- Change
- Freiheit
- Steuern
- Mobilität
- Digitalisierung
- Besser bauen
- Circular Economy
- Utopien
- Divestment
- Handeln
- Baden gehen
- Schuld und Sühne
- Wir müssen reden
- Rebound
- Sisyphos
- Gender
- Wert-Schätzung
- Glück-Wunsch
- Trans-Form
- Vor-Sicht
- Trennen
- Selbermachen
- Teilhabe
- Wachstum